Supply Chain Innovation: Building Efficient and Resilient Organizations
In recent decades the globalized economy and increased international trade have expanded supply chains across the globe, which unavoidably has brought about new dependencies. These new dependencies come with both significant benefits and risks, creating unforeseen weaknesses.
The COVID-19 pandemic exposed those vulnerabilities in dramatic fashion, showing that organizations simply were not prepared to bounce back from such disruptions.
An Accenture report showed that immediately after the COVID-19 outbreak, 71% of organizations didn’t have a backup plan for their business operations and a Gartner study reports that merely 17% of companies have supply chains that are actually prepared to handle disruptive events.
Organizations are now re-evaluating their supply chains and shifting focus from cost reduction, to becoming more resilient through redundancy.
But, going extreme in either direction isn’t the answer. Every organization must find the optimal balance between resiliency and efficiency for their specific situation. That’s where supply chain innovation comes into play.
In this article, we explore supply chain innovation and explain how you can create resilient and efficient supply chains by leveraging technology, collaboration, and process improvement.
Table of contents
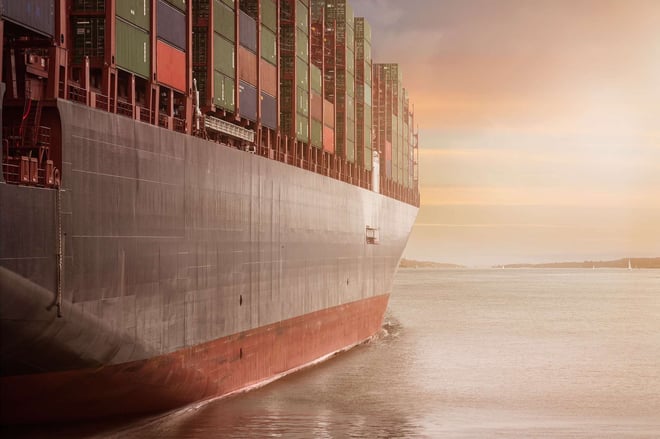
What is supply chain innovation?
To start on the right foot, let’s first define supply chain innovation, as there might be some misunderstanding or misconception about the term.
Even though technological advancements play a huge role in supply chain innovation (SCI), it’s important to note that SCI is more than that. While a simple Google search will show results on AI, drones, or robots, in fact, innovating in the supply chain has a lot to do with process improvement, collaboration, and overall management practices.
So, what is supply chain innovation?
In short, supply chain innovation refers to any changes in the elements of the supply chain that are meant to create new value for stakeholders. These can refer to new technologies, but also to process enhancement, communication, and improved collaboration.
Supply chain innovation refers to any changes in the elements of the supply chain that are meant to create new value for stakeholders.
If we go into more detail, we can make the distinction between organizational and market-level innovations in the supply chain.
For example, at the intra-organizational level, you could employ new technologies for planning and forecasting or improving processes.
At the inter-organizational level, you could innovate with suppliers, partners, or other stakeholders to develop new products – or simply make collaboration smoother.
There are different ways in which innovation can be embedded into the supply chain. For example, end-to-end supply chains have made the front pages as models to increase efficiency, minimize waste, and ensure transparency.
This is what Apple is doing, managing the entire process, from procurement to production up to delivery to the customer. Apple controls both the hardware and software of their products. Amazon, Microsoft, Tesla, Google, Nvidia, and pretty much every innovative company have a similar approach.
When a part of the supply chain becomes a major bottleneck or is a major cost center, it makes sense to take control of those parts to address the bottlenecks and turn cost centers into additional sources of growth and profit, just like Amazon has done with AWS, but also warehousing and shipping.
There’s also the localization approach. BMW is one of the many companies working to increase its localization. This is the “local-for-local” method, which aims to produce and distribute goods closer to where they will be consumed.
However, it’s good to note that this strategy is not embraced by everyone. Understandably, it cannot be the solution to all problems, as it could also work to the detriment of some markets.
The post-pandemic world brought new challenges. Next to technology, transparent network structures, communication and better processes all make for more innovative supply chains that can help mitigate the challenges of the post-pandemic world.
Let’s take a closer look at these elements and their role in innovating the supply chain.
Leveraging the Elements of Supply Chain Innovation
Supply chain leaders acknowledge the need for greater visibility across the whole supply chain and this has become a main focus for many. 83% of leaders plan to invest more in supply chain visibility, which they see as a priority, and not so much in technologies like drones or AR, the hyped terms that make the headlines.
Yet, technology is still one of the big enablers for greater transparency and visibility. But for optimal results, the three main elements of SCI: technology, process innovation, and network structures should work in sync.
For optimal results, the three main elements of SCI: technology, process innovation, and network structures should work in sync.
Technological breakthroughs, such as data analytics, IoT, automation, AI, and blockchain, have transformed supply chain operations by enabling real-time tracking, predictive analysis, improved efficiency, and enhanced visibility and transparency.
Let’s take Amazon as an example. They’ve revolutionized e-commerce in many ways, with the supply chain being a prime (no pun intended) example. Amazon is using the latest technologies to streamline its supply chain, setting a new industry standard for efficiency and resilience.
They use robots to automate various tasks in their warehouses, AI and advanced data analytics to forecast demand, improve customer experience, and for inventory management, IoT helps them track and monitor inventory, shipments, and delivery vehicles. Their cloud services support the scalability, flexibility, and security of their supply chain operations.
However, their biggest supply chain innovation is to turn these massive costs and investments into revenue-generating assets by providing others with the same tools and capabilities, for the right fee. They used technology to improve supply chain connectivity and optimize the network structures that bring together suppliers, buyers, and consumers, which brings us to our next point.
Network structures are the backbone of supply chain innovation. They bring together different entities like suppliers, manufacturers, distributors, retailers and customers. For organizations whose products are made of thousands of elements these networks can become highly complex.
While controversial in some aspects, the fast fashion brand Zara has a highly efficient supply chain network. They have a network of small-scale suppliers located close to their manufacturing facilities.
Zara has an efficient distribution as their products are shipped to the stores directly from the manufacturing facilities, eliminating the need for intermediaries. Their emphasis on speed, proximity, and agility is what enables them to swiftly adapt to changing trends, minimize inventory risks and maintain their competitive advantage.
But the more complex the supply chain, the harder it gets to maintain highly functional networks. Connecting multiple suppliers, distributors, manufacturers and retail partners requires a well-synchronized system, backed by processes such as demand forecasting, order management, supplier relationship management, and others.
The dynamic nature of these processes makes them prone to vulnerabilities, so like other elements of the supply chain, they also need to be flexible and agile. That’s why process innovation is the focus of many supply chain leaders.
Process innovation can be achieved through lean manufacturing, agile practices, integration, and supplier relationship management. These practices are all aimed at optimizing efficiency, reducing waste, and fostering collaboration.
Next to these approaches, it’s also important to regularly evaluate and optimize your processes through continuous improvement initiatives, which can bring significant long-term gains.
The most notable example of supply chain innovation is Toyota, whose production system proved to be resilient, even when most car manufacturers were hit hard. There are several factors that contribute to their successful supply chain management, and among these are the strategic approach to inventory planning, their multi-level approach to continuous improvement, their Kanban system, as well as the collaboration and trust with suppliers.
How to balance resilience and efficiency for supply chain innovation
The current trends in supply chain innovation are emphasizing the need for leaders to change their priorities and find a better balance that can enable both resilient and efficient supply chains.
Now, maybe more than ever, supply chains need to be customer-centric, to deliver value through sustainable and responsible actions. Younger generations have entered the market and their demands are different from those of their parents or grandparents. They want transparent and ethical supply chains, but they also expect more personalized products, services, and experiences.
Organizations have to adapt to changing behaviors, anticipate needs, while also address risks and reduce costs. So, three major things to juggle with.
Organizations have to adapt to changing behaviors, anticipate needs, while also address risks and reduce costs.
Striking the right balance depends on the dynamics and logic of your business. Some businesses may opt to err on the side of caution, minimizing costs and waste by keeping inventories low and accepting the occasional lost sale from having empty shelves.
On the other hand, certain companies prioritize providing a superior customer experience, for which high availability is typically important. By delivering a premium experience, they can maintain high prices and afford the extra costs involved with that.
If you want to tackle these supply chain challenges, there are strategies and approaches that can help. Let's explore some practical solutions that will help you navigate these obstacles.
1. Open and transparent intra- and interorganizational communication
Transparent communication lies at the heart of successful supply chain innovation. In fact, in their framework for more resilient global supply chains, OECD emphasizes the need to build trust through better communication and more transparency.
To achieve this inside the company, establish clear communication channels within your organization. By openly and systematically sharing updates, challenges, and progress related to supply chain operations, risks, and strategies, you foster a culture of collaboration and trust among your team.
You could also run training programs to enhance communication and collaboration skills among your supply chain teams. Remember that there is great value in retraining and upskilling employees during major transformations, so they are equipped with the necessary tools and knowledge.
Externally, aim to establish universal guidelines and channels that harmonize communication among all collaborators and suppliers across industries. By promoting standardized practices, you create a seamless flow of information, minimizing misunderstandings and inefficiencies throughout the supply chain network.
2. Develop cross-functional relationships within the organization
To be able to foster that transparent communication, you need to break down silos within the organization and develop cross-functional relationships.
In practice, this means that all teams and departments that are part of the supply chain should work together and have visibility of their activities. While these relationships are fostered through constant communication, working cross-functionally in the organizations also means jointly planning, strategizing, and executing initiatives.
To illustrate the point, if it’s just up to Purchasing to choose your suppliers, they’ll naturally choose the lowest cost option, regardless of quality or availability. Engineering and Operations will naturally make the exact opposite trade-offs. But bring them together, and you’ll find the right balance.
It’s important that all teams have a common understanding of goals, challenges, and opportunities. As leaders, you should create unified, data-driven systems that connect all stakeholders, but also maintain cross-functional relationships.
For example, P&G has formed dedicated cross-functional teams that collaborate closely with suppliers. This approach allows P&G to tap into the diverse skills and perspectives of its employees to analyze the market, discover innovative ideas, and identify suitable external partners.
Additionally, collaboration among teams within the supply chain is crucial to drive efficiencies and gain valuable insights, which takes us the next important strategy on the list.
3. Supplier innovation
Innovating with suppliers is not just about opening the organization to external ideas. It’s about deep collaboration with your supply base to maximize your joint innovation potential.
Supplier innovation is about deep collaboration with your supply base to maximize your joint innovation potential.
For this, you need a different kind of mindset, accountability, leadership buy-in, as well as an entire infrastructure and robust processes. Basically, you want processes, technology, and people to align and work seamlessly.
A very interesting study from McKinsey revealed that companies that effectively collaborate with their suppliers to drive innovation tend to outperform the competition by a factor of 2.
An example of good collaboration is how L’Oréal is fostering innovation with their suppliers through their annual “Cherry Pack” exhibition where suppliers get insights into consumer trends based on which they can develop packaging solutions aligned with the trends. This type of collaboration enables innovative ideas to flourish while strengthening supplier-buyer relationships.
Another success story is Unilever’s partnership with Novozyme that joined forces to develop more sustainable detergents. The collaboration resulted in two innovative solutions with higher performance. This enabled them to cater to a different market, premium products.
In the upcoming section, we'll explore another interesting example: Signify, their supplier collaboration program, and the convention where suppliers connect with C-suite leaders to share insights and discuss industry trends.
4. Leverage technology for end-to-end supply chain optimization
Technology enables real-time tracking and monitoring of goods, it provides comprehensive visibility across the entire supply chain. At the same time, it can help you leverage data analytics to make informed decisions, and automate processes for proactive management, demand forecasting, inventory maintenance, and quality controls.
Greater communication across the whole supply chain can minimize the bullwhip effect, and technological advancements like AI, and real-time analytics allow for faster response time and fewer errors, reducing the effect even further.
Here are some key technologies that enhance collaboration and communication:
- Cloud-based Collaboration Platforms that provide a centralized environment for stakeholders to communicate, share information, and collaborate in realtime. They can be used either inside the organization or for external collaboration with suppliers.
For example, Ennustepankki is a forecasting platform that automates demand forecasts in the food industry. We’ll dive deeper into this example in the next section, but Ennustepankki showcases how cloud-based platforms can be used to share information and enhance collaboration. - The Internet of Things (IoT) enables the collection and sharing of real-time data throughout the supply chain. Sensors and connected devices can monitor inventory levels, track shipments, and provide valuable insights into the status and condition of goods days or even weeks earlier than with traditional methods.
- Enterprise Resource Planning (ERP) Systems are used to manage day-to-day activities like accounting, procurement, project management, risk management, etc. While some ERPs have supply chain management and supply chain planning capabilities, going for an all-in-one solution is often not ideal, especially for larger organizations with highly complex supply chains.
For such cases it’s typically best to have dedicated SCMs integrated with their main Enterprise Resource Planning system. They offer advanced capabilities like demand forecasting, transportation optimization, warehouse management, and supplier collaboration, tailored to address complex challenges. Assessing your specific requirements and evaluating available options in practice will help determine the best solution for your needs. - Supplier Relationship Management (SRM) Systems facilitate effective supplier management allowing buyers and suppliers to interact, manage contracts, track performance, and collaborate on sourcing and procurement activities.
5. Embrace a culture of continuous improvement:
All these technological advancements sure help bring both efficiency and resiliency in the supply chain, but to get to implement them and draw the benefits you need a systematic approach as well as a culture of continuous improvement that strives to constantly improve on existing processes.
A survey among supply chain leaders recently revealed that 85% of respondents define innovation in their organization as “process improvements” or “business model innovation”.
There is a significant shift in how innovation is approached in the supply chain, especially if we look back at the trends that governed supply chains more than twenty years ago.
85% of respondents define innovation in their organization as “process improvements” or “business model innovation”.
Today there is clearly a better understanding of the important gains brought by incremental improvements. To succeed, you should focus on improvements that lead to long-term gains, and then systematically work to increase your pace of innovation.
For this, there are two primary methods. First, you can simply work on all the obvious improvements, that don’t require detailed planning or testing, across the entire supply chain. These usually provide a good ROI and allow you to move the needle quickly.
Alternatively, you can go after bigger and more ambitious challenges by breaking them down into smaller chunks. Here you’re looking to keep moving in the right direction and make a difference, one step at a time, but also to learn how to best tackle these big challenges. In these cases, you simply can’t really plan your way to success in the comfort of your PowerPoint or Excel documents.
For example, you can start by identifying a specific process that needs to be improved. Look for something that can be implemented and tested at a small scale within a timeframe of 30-90 days. This test should deliver real results, but also help you learn how to scale up or reevaluate the process.
Look for something that can be implemented and tested at a small scale within a timeframe of 30-90 days. This test should deliver real results, but also help you learn how to scale up or reevaluate the process.
Also, encourage continuous learning and keep up with industry trends and best practices. By actively seeking knowledge, you can identify opportunities for improvement and innovation within your supply chain operations.
Additionally, establish mechanisms for feedback and idea sharing between different teams in the supply chain. Frontline employees, those working in logistics, deliveries or other customer-facing roles always have plenty of tacit knowledge that can be turned into valuable opportunities for improvement.
If you want to learn more about building a continuous improvement culture in your organization, we have an extensive guide that can help you in the process. And because there is no better day to start than today, you can start your continuous improvement initiative using a dedicated Viima board template.
Examples of Successful Supply Chain Innovation
By now, you’ve probably noticed that there is no single ‘correct’ way to do supply chain innovation. To get some clarity, as well as inspiration on how you could approach this in your organization, let’s have a look at some companies that have successfully brought innovation in their supply chain.
None of the examples will be a silver bullet that solves all your problems, but examining the success stories of companies that have effectively implemented supply chain innovation can provide valuable insights.
Nike
Nike has completely transformed the game when it comes to their supply chain, putting digital at the forefront of their operations. After the COVID-19 pandemic, Nike took important steps to revolutionize their supply chain, ensuring they could better serve their customers while also prioritizing sustainability.
One of their moves was the establishment of regional distribution centers in the US and across Europe which help them boost capacity, speed, and precision. These strategically placed distribution centers brought them closer to target markets which reduced transportation time and costs. They also established advanced inventory management systems, allowing for real-time data tracking and analysis which enhanced visibility and lead to better forecasting, planning and demand prediction.
And finally, with regional distribution centers, Nike had the flexibility to adjust inventory allocation based on real-time demand signals. They could quickly respond to regional variations in consumer behavior, optimize inventory levels, and allocate products where they were needed the most.
But Nike understood that it’s not just about the tech wizardry. Their biggest competitive advantage lies in their employees, which they value and recognize as the force behind their operations. This is a great reminder that while technology can do wonders, it's the people behind it all who choose the right innovations to pursue and truly make the magic happen.
If we take a step back and we look at the bigger picture, this embodies perfectly the Triple Bottom Line framework, which aims to balance social, financial and environmental aspects, so People, Profit, and Planet.
COSMOPlat
Haier, the multinational consumer electronics, and home appliances company initially created the COSMOPlat platform for internal procurement functions. Over the years it evolved into a more complex tool that facilitates collaboration with external stakeholders and increases their supply chain agility.
COSMOPlat has now become both a supply chain management system and an innovation engine that enables collaboration between different stakeholders. At its core, the platform is using big data, artificial intelligence, IoT (Internet of Things) to create an ecosystem, where real-time monitoring and analysis take place. This increases their efficiency flexibility and customization.
The platform is used in 20 countries, with significant success and benefits for their production efficiency, reduced stockout rates, faster receipt of payments and increased capability for product customization.
The interesting thing about Haier’s COSMOPlat is that, unlike other platforms or companies that engage with suppliers, they don’t control the collaboration process and don’t limit access only to their suppliers. Haier posts a problem they face and suppliers come up with solutions.
Even though building a platform like COSMOPlat is not for every company, there are still other ways in which you can enhance collaboration among suppliers and create your engine for innovation, even at a smaller scale. This is how Signify started their supplier collaboration process which has now become their own innovation engine. Let’s see how they did that.
Signify
Signify is at the forefront of innovation in the lighting industry and to stay innovative they promote cross-functional collaboration and leverage suppliers’ knowledge during product and process development.
To achieve this, they put in place the SEED program, an exclusive and collaborative initiative, aimed at creative ideation and co-creation, where only the best suppliers are selected and invited to participate.
As the program evolved and they needed a structured approach to work with their suppliers, they wanted an innovation management platform that would help run the process and allow for transparent collaboration. They decided to use Viima so they didn’t have to build anything new to cater to their ecosystem. It was easy to use both internally and by external parties, so people were more engaged to contribute and collaborate.
With a dedicated platform, they were in control of the development process by only inviting the best suppliers that meet their high standards for quality and performance.
Ennustepankki:
Ennustepankki is a multi-tier sharing and forecasting platform developed by CGI and Relex that aims to innovate the supply chain in the food industry by automating demand forecasts for raw materials based on the planned menus of large-scale caterers and food service companies.
Traditionally, food manufacturers and wholesalers received purchase orders, and perhaps some menu plans, from food service companies. They, in turn had to share their planned menus and forecasts with different suppliers and producers individually.
Ennustepankki addresses this challenge by collecting information from the systems of large commercial kitchens, where menus are planned weeks in advance. It compiles a forecast that combines the quantities of products and ingredients ordered by all kitchens, making production and purchasing planning much easier across the supply chain.
One of the main benefits of Ennustepankki is that it brings much-needed transparency to unexpected spikes in orders, helping wholesalers and manufacturers better match the demand, and the food service companies to get the right amount of ingredients on time.
Centralizing the forecast information reduces manual work dramatically, improves communication between different stakeholders, and cuts waste at all levels. Everyone in the industry wins by participating.
Conclusion
After this insightful journey, let's recap and summarize the key takeaways for achieving resilient and efficient supply chains capable of overcoming current and future challenges.
Supply chain innovation can take place both at the intraorganizational level through technological advancements and process improvements, and at the interorganizational level through collaborations and partnerships with suppliers.
These aspects are brought together by three crucial elements: technology as the backbone of innovative supply chains, continuous improvement throughout the entire supply chain, and network structures driven by transparent communication and end-to-end visibility.
There are five main strategies that can help you achieve the right balance between resilience and efficiency:
- First, prioritize transparent communication internally and externally, engaging with stakeholders at every level.
- Second, cultivate cross-functional relationships to ensure seamless collaboration among all supply chain teams.
- Third, collaborate with suppliers on innovation initiatives, leveraging their resources and capabilities.
- Fourth, harness the power of technology to transform your supply chain into an innovation engine.
- Lastly, embrace a culture of continuous improvement to secure long-term gains for your supply chain.
Now armed with this knowledge, it's time to take action, one step at a time, and start building resilient and efficient supply chains that can withstand the challenges of today and tomorrow.
If you work in the supply chain and want to improve visibility through effective communication and collaboration with stakeholders, explore our ready-to-use board templates. The templates are designed to streamline your processes and can be customized to fit your needs, allowing you to kickstart your initiatives in no time.